X
Making Metal Matter
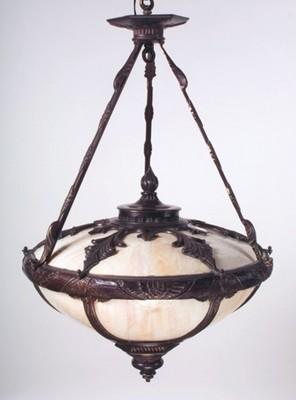
Bend it, mold it or cast it. Use bronze, silver, gold, aluminum or iron. It doesn’t matter. As long as it is made of metal, Gladstone Industries can create it.
The Los Angeles area-based foundry recently opened a Las Vegas showroom to display its myriad products which include lighting fixtures, staircase railings, fire screens, furniture, gates, door pulls and hardware.
"Whatever the customer wants, we can make it," said Vicki Atlasman, president.
Prominently featured in the showroom are a variety of chandeliers and lighting fixtures, one of the firm’s specialities. Atlasman estimates that about 60 percent of the company’s business is light fixtures of one type or another.
What sets Gladstone apart from other foundries, aside from its vast repertoire of decorative architectural work, is its ability to work in any type of metal, which Atlasman said is rare to find.
She said her staff is trained in all aspects of metal work including lost wax and sand casting and hand-forged wrought iron.
The company can create original designs or recreate designs from photographs or drawings, Atlasman said. Gladstone has an artist on staff who specializes in old-world designs and a design engineer, whose creations are more contemporary.
"I really hate to say we have just one artist on staff," she said. "It takes a lot of artistic talent to see a design (on paper) and then shape metal into that design."
Each piece is customized to a client’s exact specifications, Atlasman said.
Diane Taylor, who manages the Las Vegas showroom, said it is not uncommon for the company to create one design for coach lights and have it resized to create wall lights, a large hanging light and lamp post lights.
And because everything is custom, clients can select everything from the metal a piece is made out of to the type of glass used and the number of bulbs required. Customers also can specify whether they prefer a regular or candle base for their light bulbs, Taylor said.
Gladstone has been certified by Underwriters Laboratories to meet safety standards so it can offer completed, working light fixtures, not just the metal frames.
To begin a project, either Atlasman or Taylor meets with the client to discuss his or her needs. Clients also are presented with a notebook filled with past works, which Taylor said is really more of a portfolio than a catalog.
From there, drawings of the project are created. Roman Galstyan specializes in artistic drawings done by hand, while Doug Carson focuses on three-dimensional computer-generated drawings. The drawings are refined over a period of weeks until the client is completely satisfied, Atlasman said.
The intricacy and amount of details specified for each piece generally determine how it will be made. According to Atlasman, the most detailed pieces are created through a lost wax process that involves having molten metal poured into a wax mold that melts away.
There is no minimum order, but naturally it is more cost efficient if a client orders a larger quantity of the same item, Taylor said, noting that the company works with both residential and hospitality-industry clients.
Atlasman began the business after spending several years running a sheet metal shop. She started with manufacturing metal parts for the aircraft and aerospace industries.
"Really, the manufacturing process is kind of the same," she said.
The primary difference is the end result. When manufacturing parts, Atlasman never gets to see the final product, something she truly enjoys with the decorative items her company makes.
"Still, it was exciting that we did parts for the space station," she added.
She admits that at first there were some challenges earning credibility in the male-dominated field. With the decorative aspect of the business, she said being a woman is more of an advantage because so many interior designers are also female.
She said one of the most fascinating aspects about her work is that it uses both the very latest technology to create designs as well as casting methods that the Egyptians used 3,000 years ago.
Taylor, who first learned of Gladstone when she was helping clients with their lighting needs, said she is continually impressed with the quality of work the company’s staff of about 40 produces. That and the company’s dedication to its customers prompted her decision to change jobs.
The Las Vegas showroom is located at 7485 Dean Martin Drive. For additional information, visit the company’s Web site at www.gladstoneindustries.com.