X
With a little skill, DIYers can get professional-looking wood floors
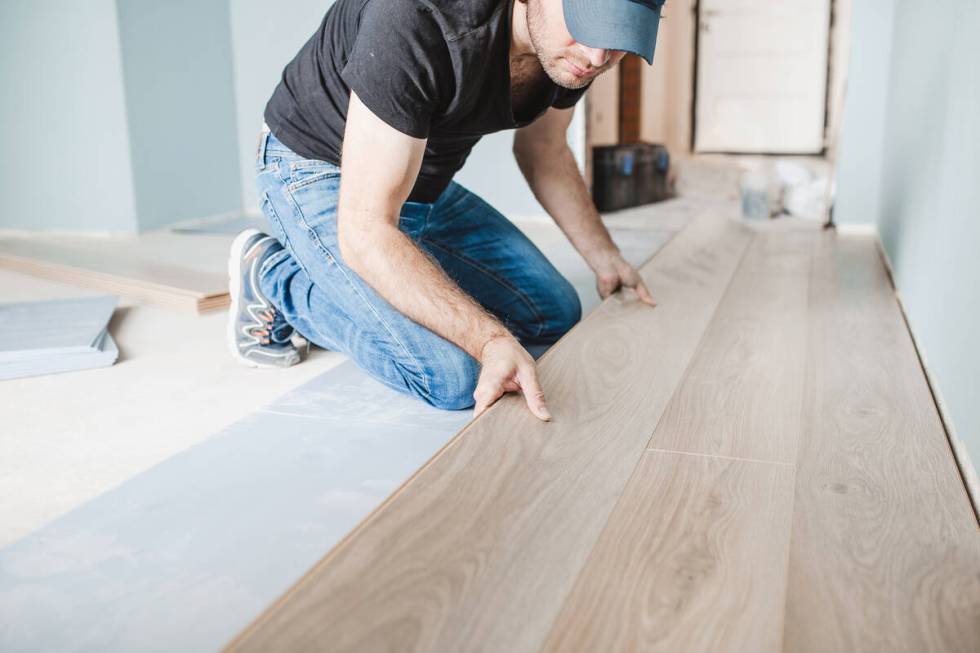
Q: I want to install a wood floor over a concrete slab in my downstairs bedroom. What kind of flooring material is needed, and how do I install it?
A: Wood floors are beautiful and, with intermediate carpentry skills, can be installed with professional-looking results. There are many choices in flooring material. Laminated floors are less expensive than real wood (usually starting around $2 per square foot) and can carry a 20-year warranty.
When you talk about real wood floor products, you can choose solid flooring material or engineered flooring. They are similar in price (usually starting around $4.50 per square foot) but have different applications.
A solid wood floor should be predrilled and nailed to the subfloor. The nails are hidden by driving them in at an angle in the tongue portion of board.
Engineered floors offer a real wood surface (about one-eighth of an inch thick) that is glued to several underlying layers of stable material. Both types of flooring use tongue-and-groove assembly, which makes for a quick, even installation.
Engineered floors over concrete can be edge-glued and floated, or edge-glued and glued to the surface of the concrete. Floating is when the flooring is edge-glued, but not glued to the surface of the subfloor. It usually rides on top of a thin foam material, which is put down before the floor is edge-glued.
Since you are installing a wood floor over a concrete slab, I suggest using engineered flooring. If you prefer a solid wood floor over a concrete slab, you should first secure a three-quarter-inch wooden subfloor to the slab, then nail the solid wood floor to it. If you decide to do this, you’ll have a significant change in the flooring height as you enter the room.
Many people believe a solid wood floor has a longer life than an engineered floor, but this is not necessarily so. The thought is that an engineered floor has only a thin layer of material that you could refinish, while solid floors could be refinished until you reach the subfloor. And don’t forget about those pesky nails, since they lie only about one-eighth of an inch from the surface. In this light, both types of floors have the same thickness of wood that can be resurfaced.
Another issue is whether to use strips or planks. The width of each depends upon the manufacturer, but basically a plank is wider because it’s made up of several strips.
Let’s say you have a plank that is made up of three strips. The plank flooring would be installed three times as fast as the strip flooring. However, some people don’t like the look of planks because the seams are not uniform. In other words, with strip flooring you’ll have a seam on every strip but with plank flooring, you’ll have a seam on every third strip.
After you’ve purchased the flooring material, place it in layers in the room where it will be installed. This will let the air circulate around it and let it acclimate to the temperature and humidity in the room. Let it sit there at least three days before installing it.
Another decision you’ll have to make is whether to remove the baseboards or keep them and use a quarter-round molding to cover any gaps. If you leave the baseboards on, you can’t be as sloppy with your measurements.
Usually, you’ll start along the longest wall and secure a starter strip with either glue or nails. If you’re surface-gluing, a 5-gallon bucket (enough to cover about 300 square feet) will cost about $60. Apply it with the recommended trowel, but give it five minutes to firm up once you put it on the floor. This will keep the boards from sliding around too much during installation.
A word of caution: This stuff is really sticky. Always have a wet rag ready to wipe off any glue that gets on the finished floor, and if you get any on your skin, you’ll be wearing it for several days.
Start at the left side of the wall and move to the right. When you come to the end of the wall, measure and cut the piece to fit. Buy, rent or borrow a power miter box saw (aka chop saw) to make the cuts at 90 degrees.
Use the leftover piece from the cut (assuming it’s at least 8 inches long) as the first strip on your next row. If the leftover piece is less than 8 inches, cut a full-length piece in half. There are benefits to this: There will be very little wasted material, and the strips will be offset (the ends of neighboring strips won’t be aligned), which will give the floor strength as well as beauty.
If you must go around corners, a coping saw works wonders. This handsaw costs less than $25 and has a thin blade that allows for cuts with a tight radius.
When you come to a corner, use a piece of cardboard and make an actual-sized template. Transfer the template to the wood floor strip and use the coping saw to cut the piece.
A table saw is also important. When you get to the last strip in the room, chances are it will be too wide to fit properly. Measure the width of the area you need to cover and rip the board to the proper width. (“Ripping” a board refers to cutting it lengthwise.)
Finally, install a new transition threshold at the entry to the room. For less than $30, you can find a transition from virtually any flooring material to match your new floor.
If you removed the baseboards, now is the time to reinstall them.
If you kept the baseboards, buy some quarter-round molding to hide the gaps between the baseboard and the floor.
Mike Klimek is a licensed contractor and owner of Las Vegas Handyman. Send questions to handymanoflasvegas@msn.com or 4710 W. Dewey Drive, No. 100, Las Vegas, NV 89118. Visit handymanoflasvegas.com.